Barn Find - 1969 Ammco Brake Lathe
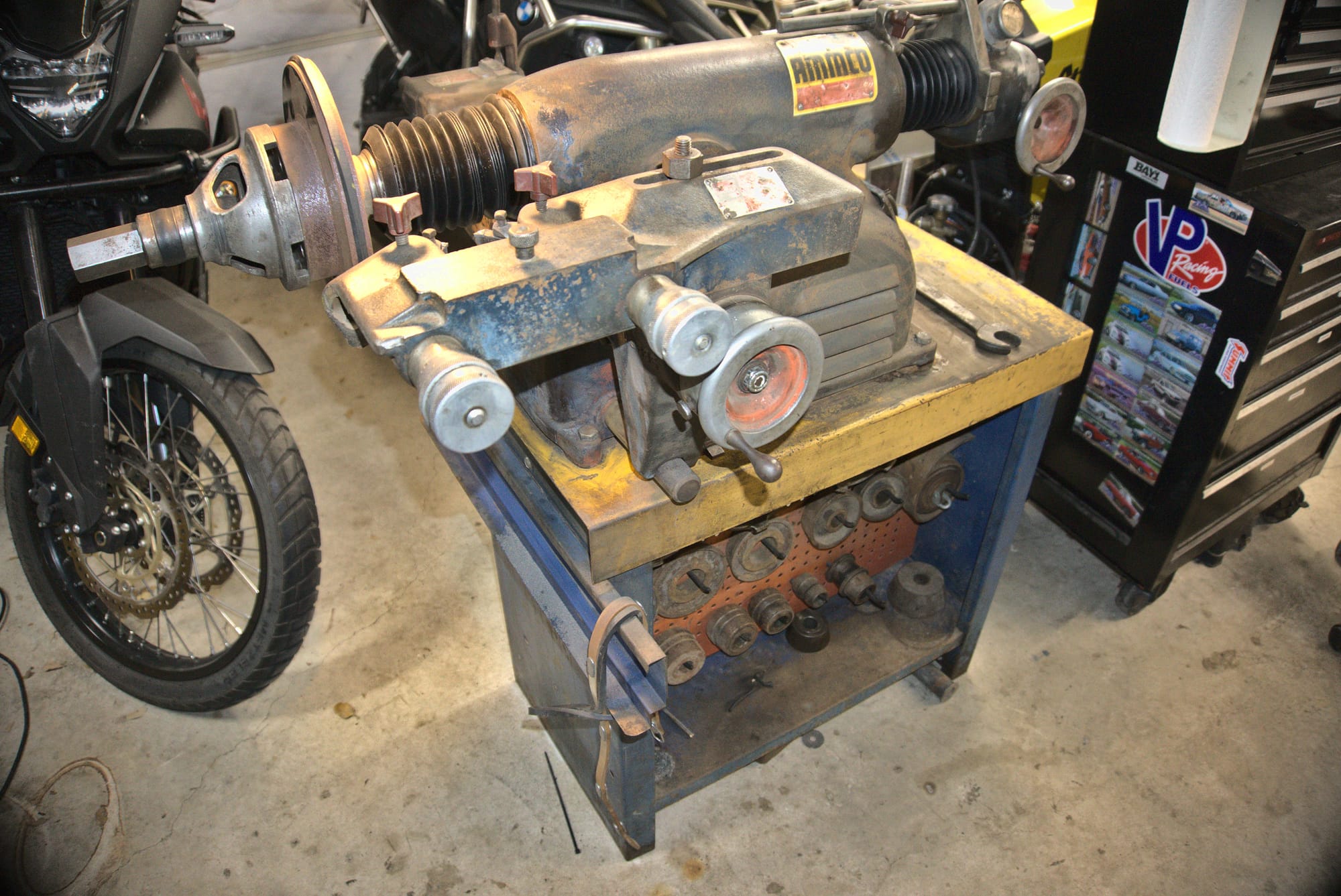
They don't make them like they used to. Seriously...
I stumbled across this particular machine in an older gentleman's barn. It had belonged to his father who ran an automotive shop some 40 years prior. Despite being covered in decades of spiders, rust, and dust, you could tell it had more to give. After confirming the shaft was straight and all of the tooling was present for drums and rotors, we loaded it and I became the proud new owner of this baby. Did I mention it weighs about 400 lbs?
Based on the first two digits of the serial number, the core machine appears to be a 1969 model. Interestingly, the disc brake auto feed tool looks to be from 1987 - potentially a later addition. Imagine - it's 1987, brand-new Buick Grand Nationals are prowling the streets and your mom’s Civic has front disc brakes. Your lathe can't cut rotors yet. You flip through a catalog, call up your local Ammco dealer, and order the latest rotor cutting tool. That's what I imagine the owner of this machine was doing at least.
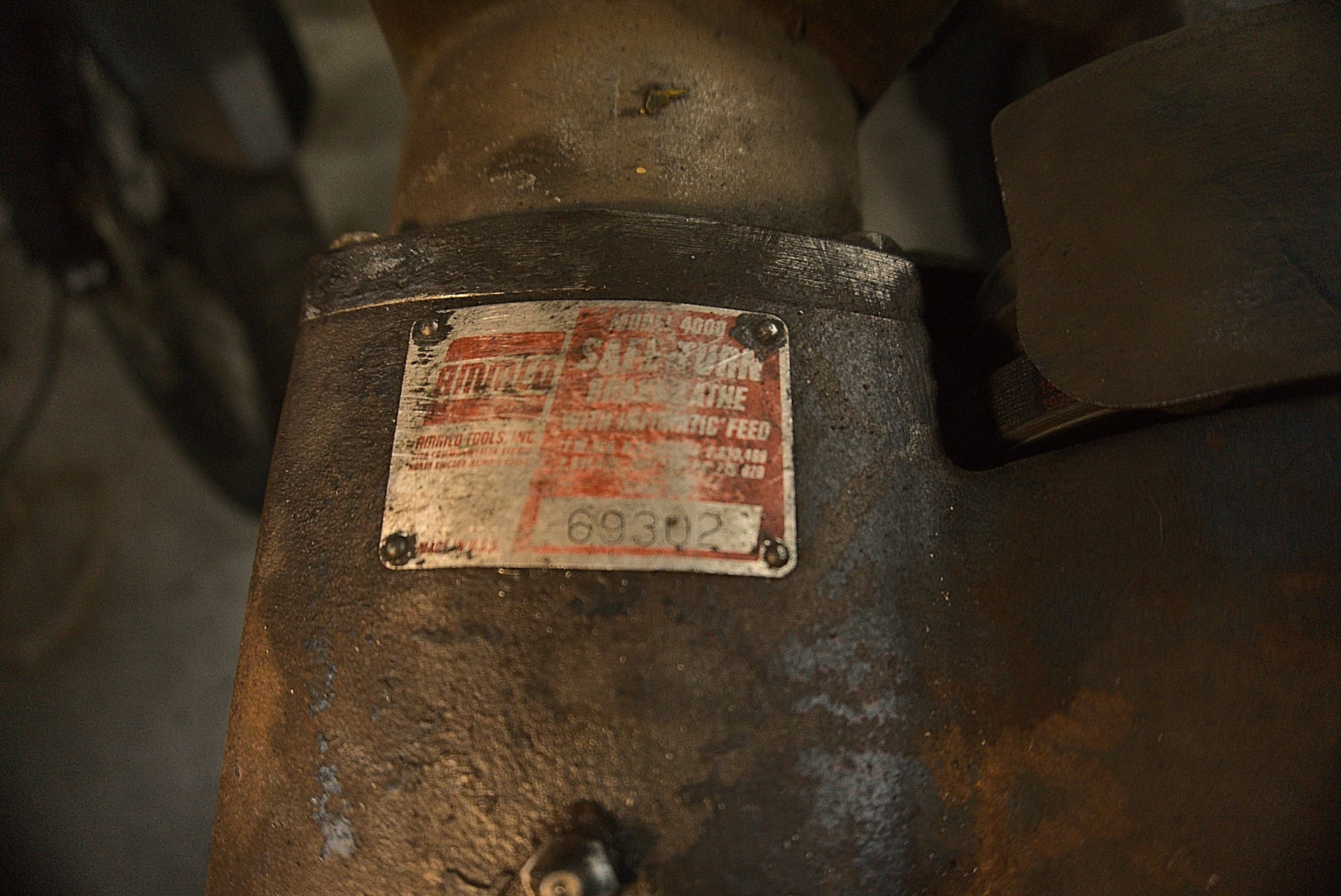
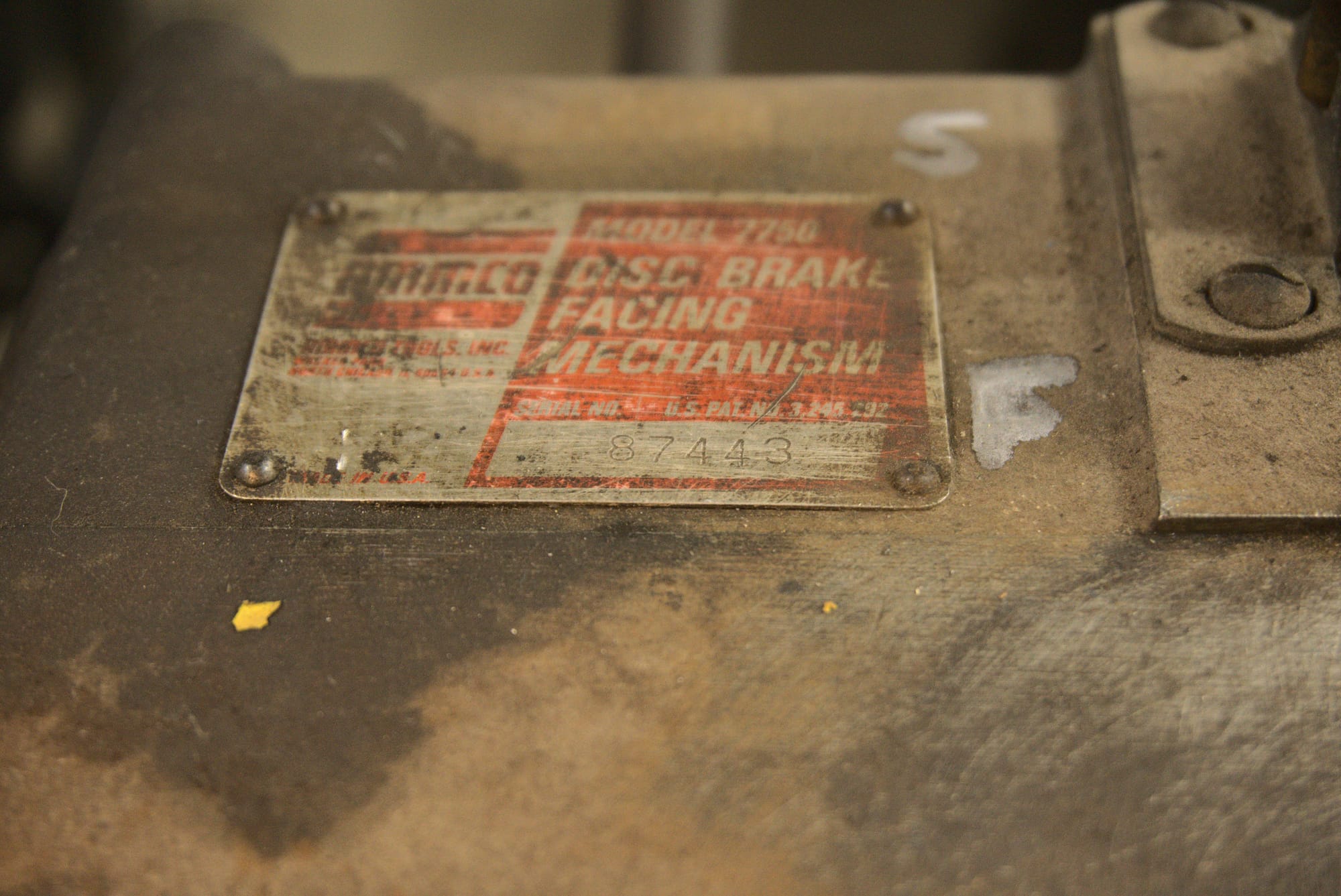
Repairs
I ordered up some of the consumables - a new set of boots, cutting tools, and belt. These were sold for decades with minimal changes, so parts are surprisingly easy to come by. Everything is made to be disassembled and rebuilt - common place for 1969 tools. What a breath of fresh air. I replaced those old boots, installed the new belt, cleaned and lubricated the spindles while in there. A small retaining ring was missing on the cross feed spindle, so I drafted one up and 3d printed it. File is here if you need it.
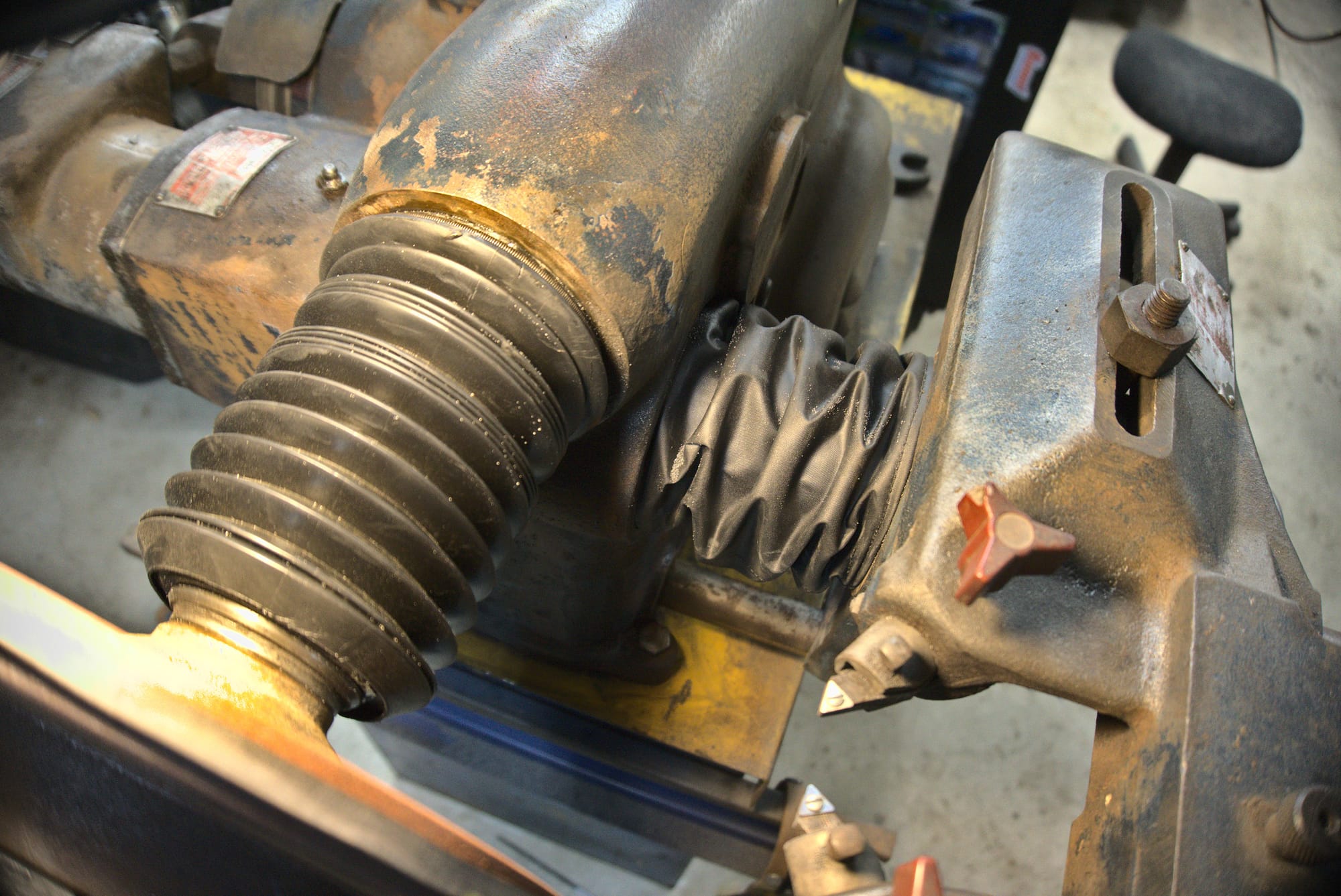
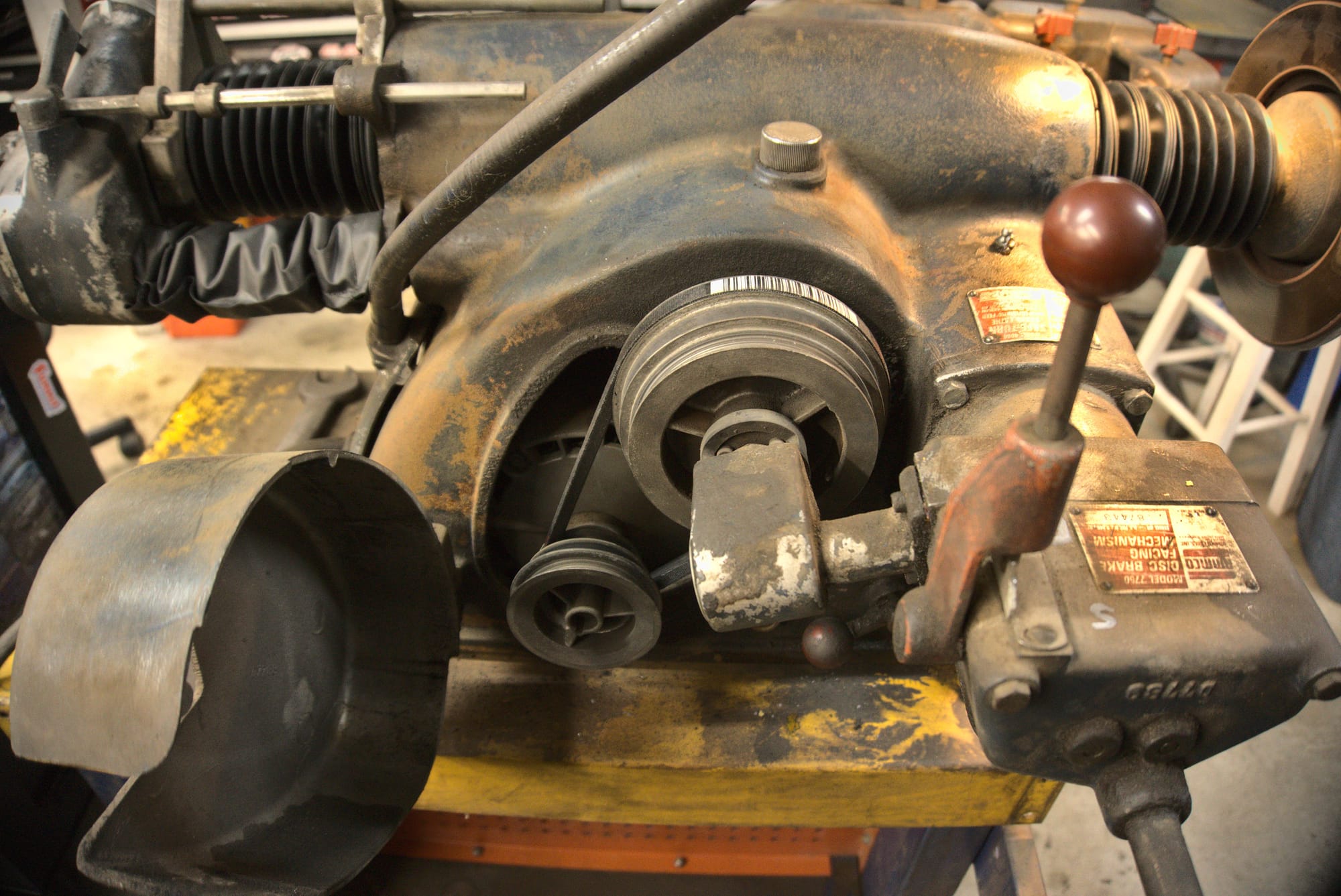
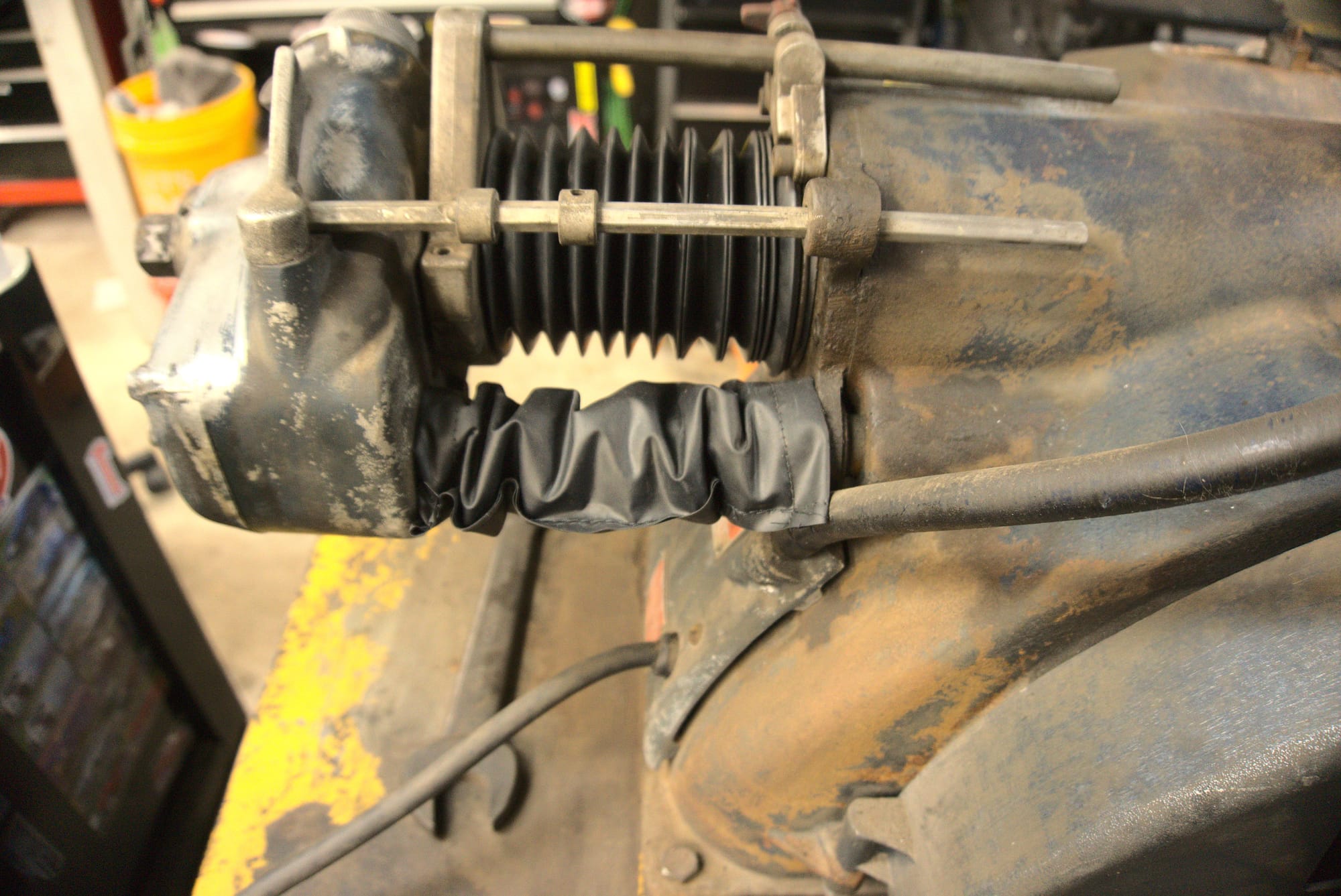
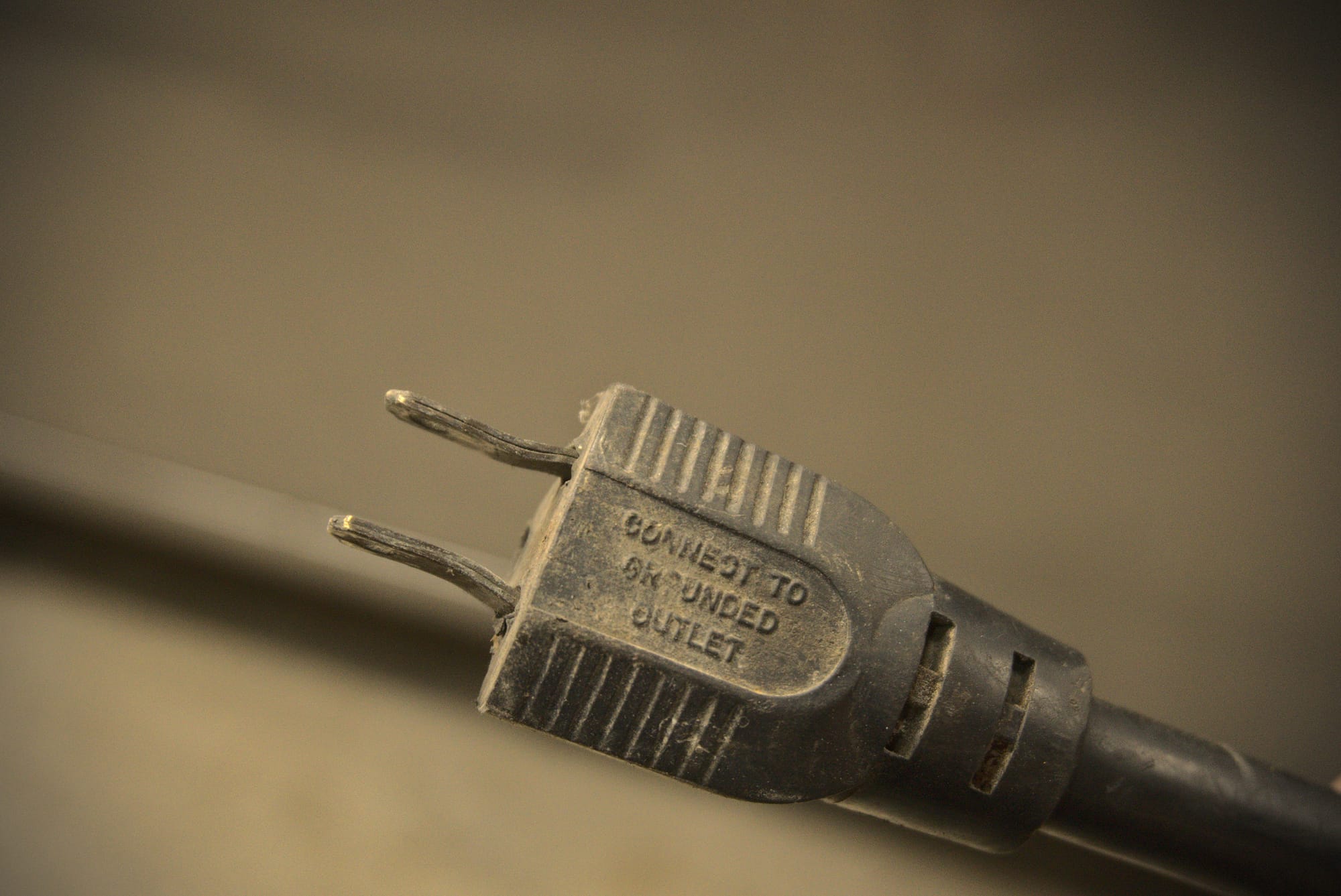
Lathe vs The Worst Rotors I've ever Had
My Honda Insight's rotors were badly warped after a trip to the Tail of the Dragon. Perfect test material! The first step was wire wheeling any rust off the surface. Then, scratch cuts are made to ensure concentricity after resetting the rotor's fixturing. Everything looked parallel and my micrometers told me I had plenty of thickness remaining, so it was go time. The manual says not to take cuts of <0.004 inches due to heat issues. I touched off, wheeled in 0.004 inches, then hit the autofeed. Exciting!
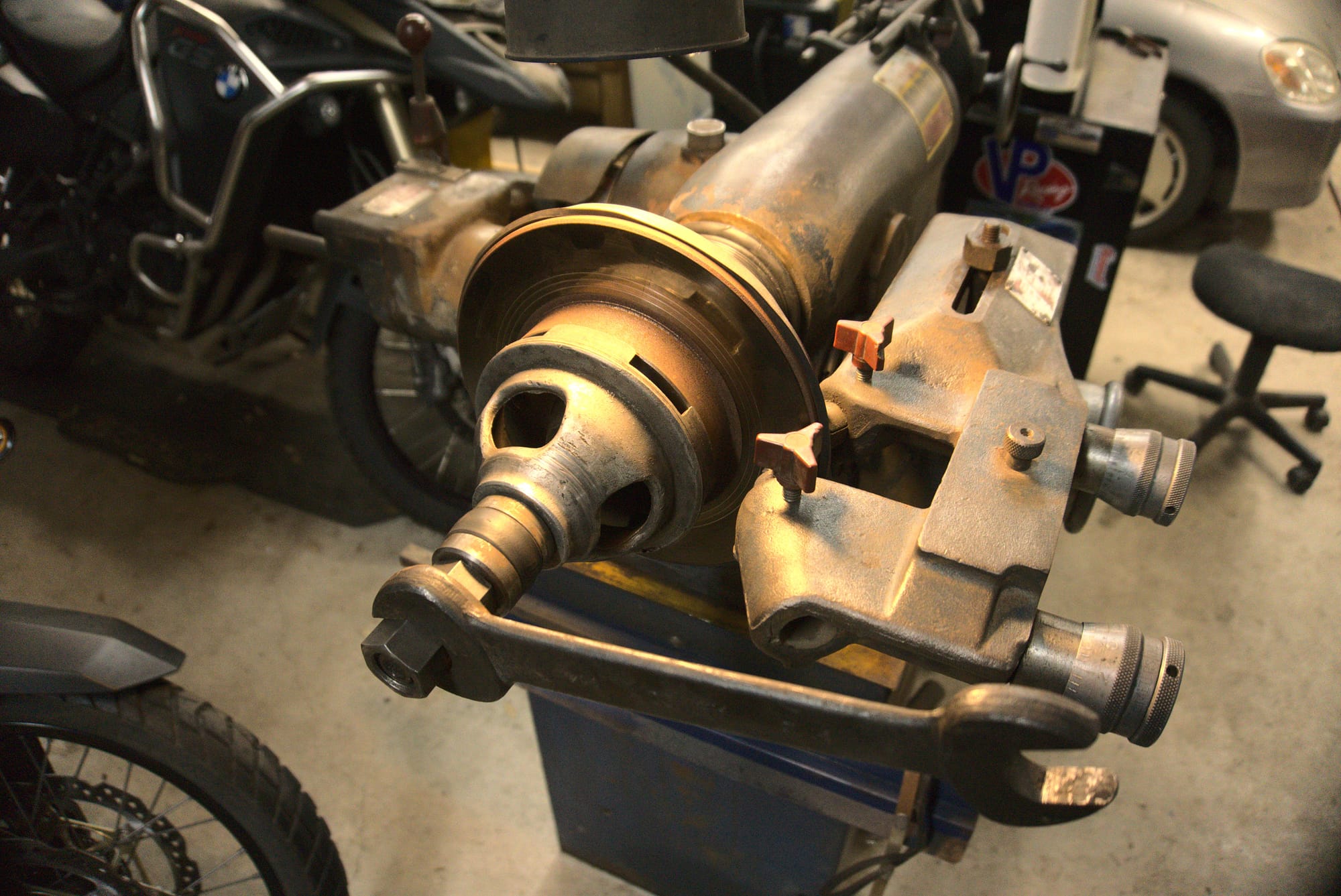
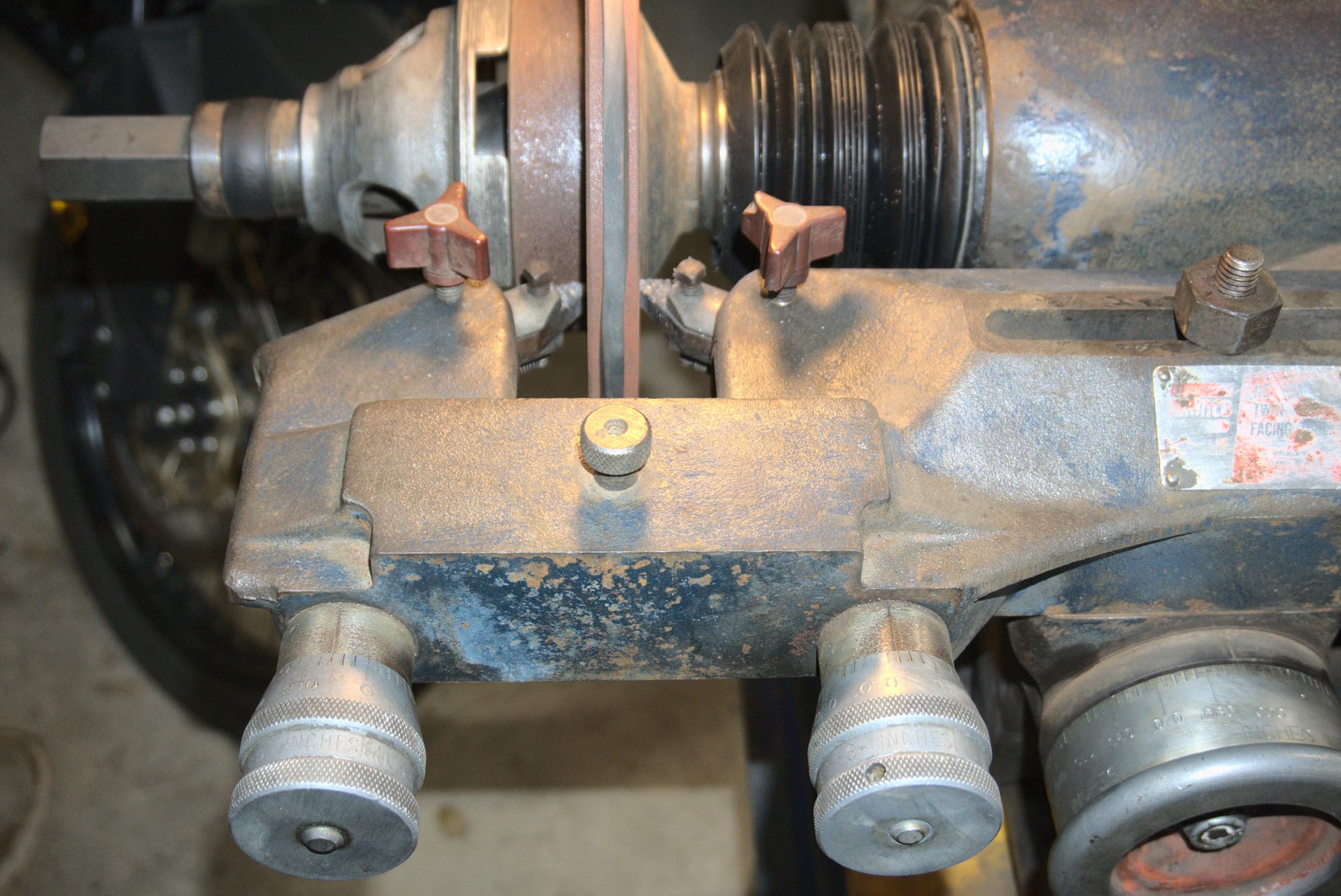
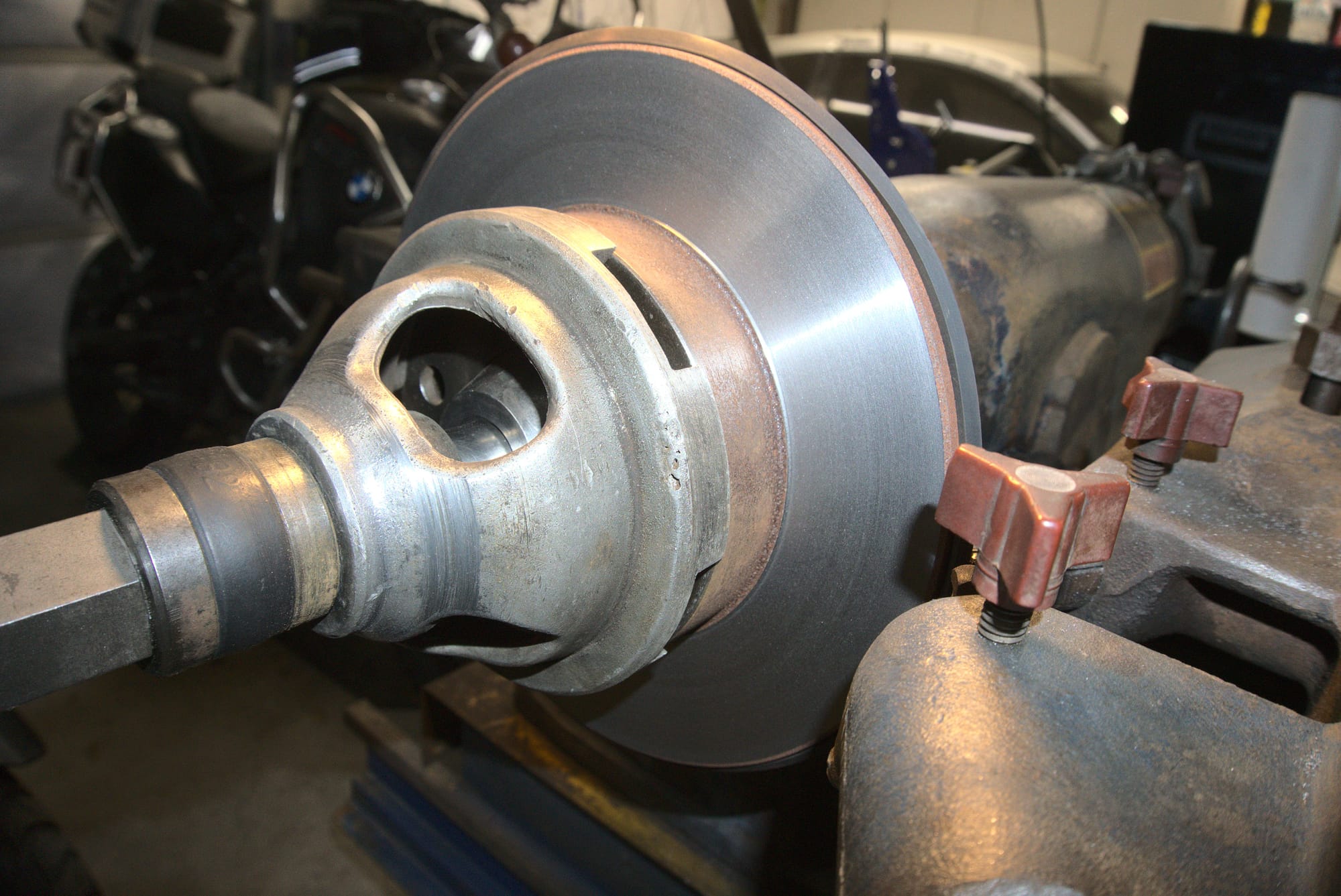

Almost good! The inside surface had a few low spots that didn't get machined, so I made an additional final pass for the finished surface.
The results were excellent! My horrific brakes now felt smooth and new. Gone with the glazed, warped surface. This Ammco machine might be old, but it's as capable as ever.
Why Shops Don't Bother
Truth is, there’s a reason shops don’t do this anymore. It’s slow. A single pass can take 5 to 10 minutes, depending on feed speed. Add in setup, cleanup, another pass or two, and you’re easily looking at 30 minutes per rotor. Why spend the time when you can sell a customer a cheap new rotor and call it a day?
What if I want to? It's fun, it's way less wasteful, and it's actually pretty inexpensive for the right person. The machines that formerly cost $10,000 new can be had for $500 on the used market now. You could justify that with one expensive set of saved rotors.
This machine is rad—it represents an era when things were designed to last. It’s purpose-built from a time when people cared for their belongings. Tools were built with real thought behind how they'd be serviced over decades—not tossed out after a few uses. It might seem obvious that a repair tool should, in itself, be repairable - but that's non trivial with modern machines. It’s a glimpse into a pre-internet world, before the age of throwaway devices and planned obsolescence. Everything about it screams keep using me, keep fixing me, I'll be around, I want to.
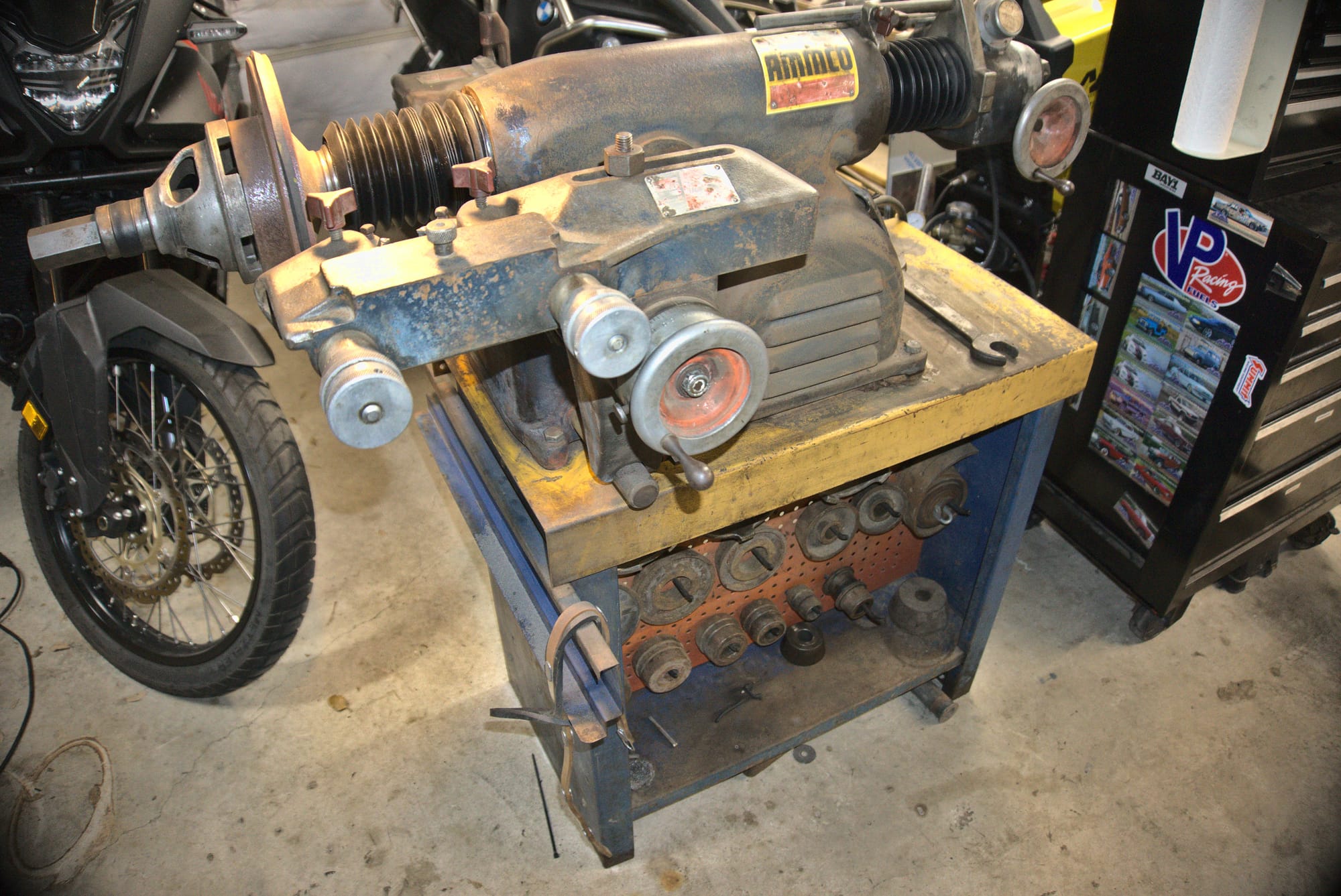