RX8 Tuft Testing
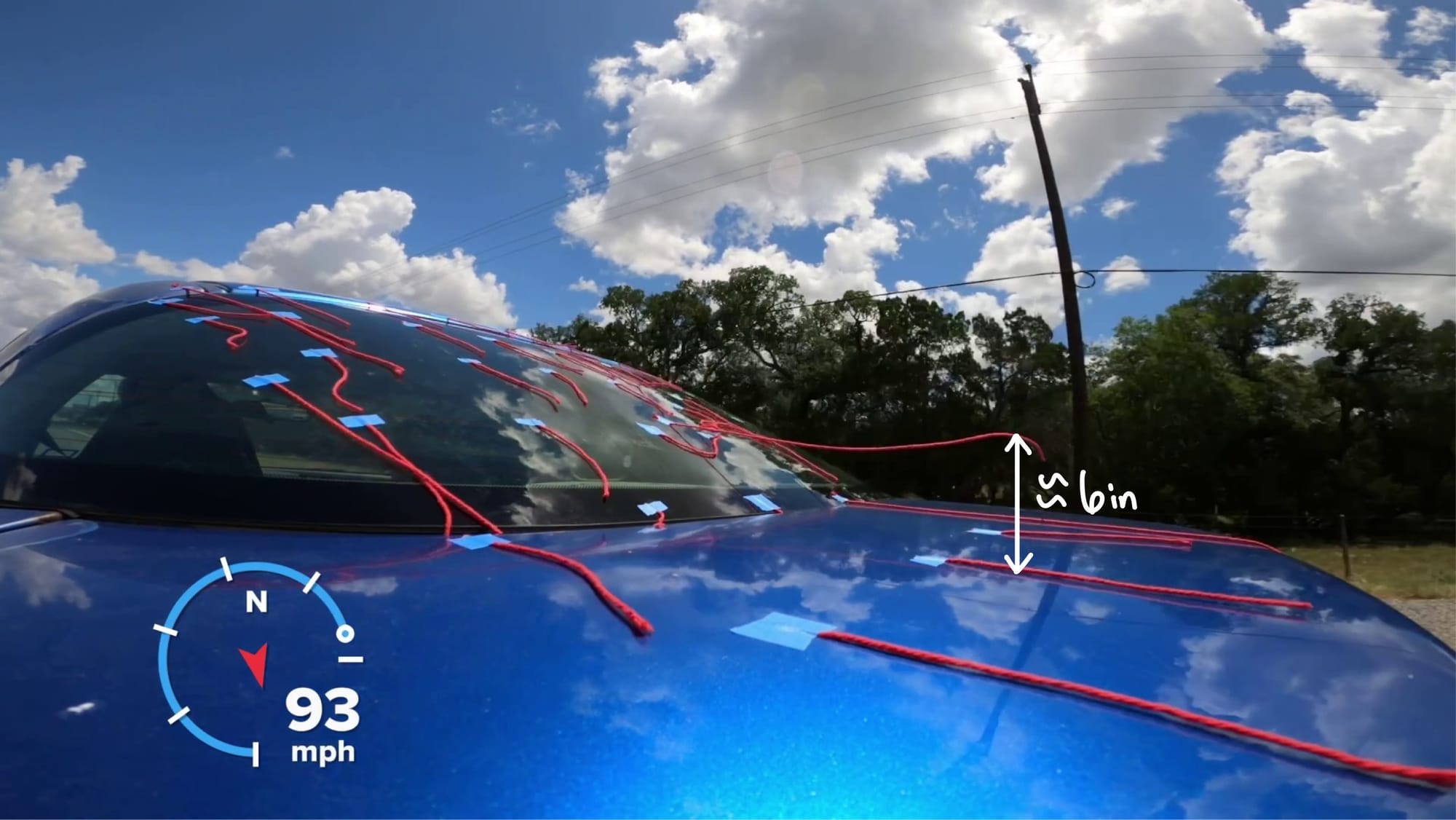
A few days ago, my buddy and I were headed home from the General Motors wind tunnel in Detroit when we decided a more accurate test should be done. Forget 3D scans and Openfoam, pressure taps or anything silly like that. We grabbed $1.79 worth of yarn and painters tape and got to work.
What was observed?
A lot of rudimentary things that will need verification. I'm putting this here for others to draw conclusions and observations. Aerodynamics is a complex, multi faceted science that I wouldn't dare to say I understand. I'll be slow to make any conclusions or generalization here. Here are the basic things I observed. Take it with a grain of salt.
-First off, the rear of the car performed surprisingly well. Flow remained well attached up to at least 50 mph.
-Above 50mph, separation becomes visible toward the lower middle of the windscreen (between the deck lid and the glass). The same is not observed about the edges. Perhaps the tapered sides are very effective.
-Above 80mph, a bubble is easily observed. It's prominent approximately 6 inches above the deck lid. This will bring along a big pressure drag penalty.
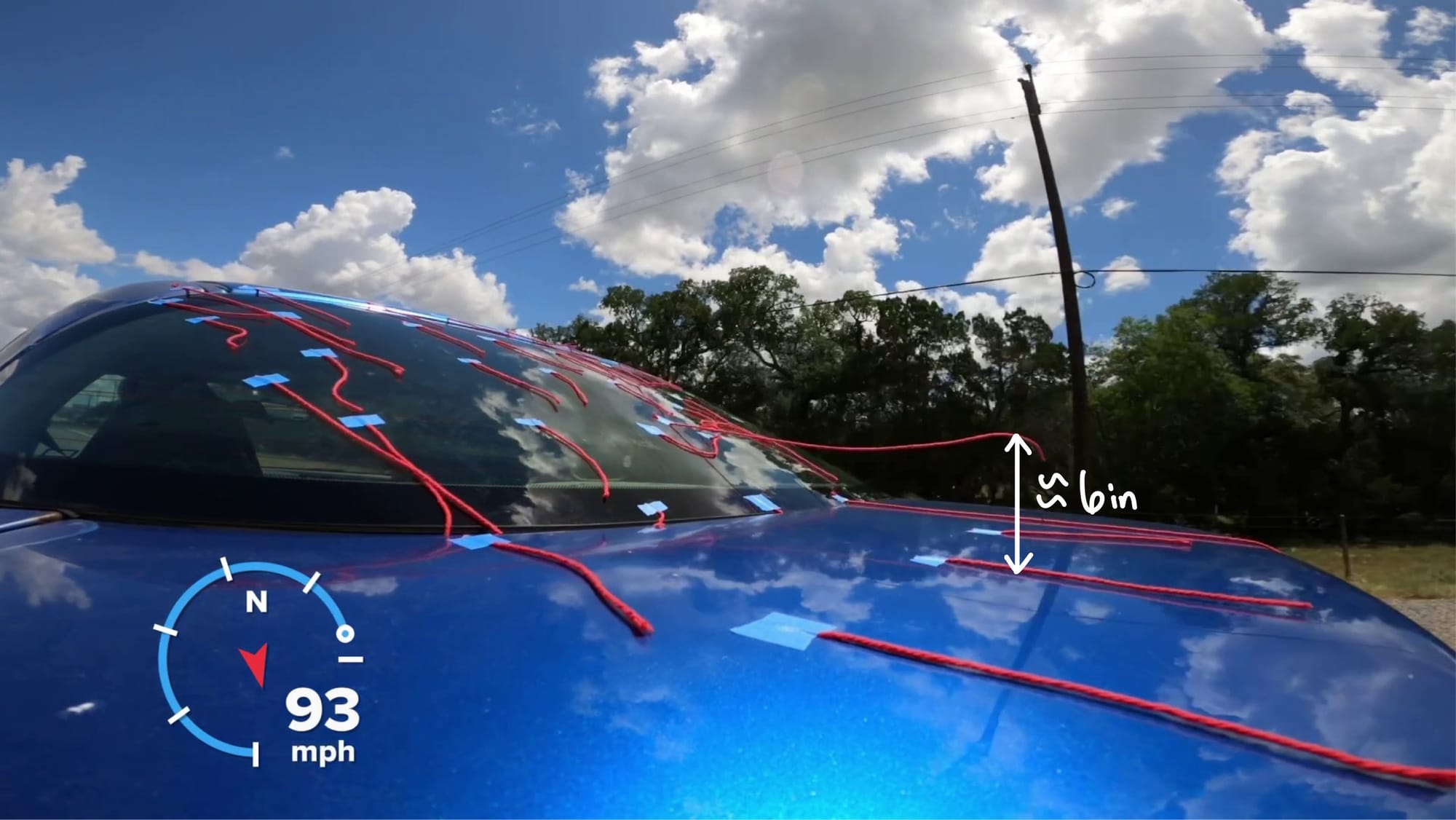
This was mostly done for fun, however it did provide a basic understanding of the performance, and perhaps where a rear wing could be placed. For a car that sees road course speed, I'd want the leading edge of an airfoil outside this area- but you probably don't need to place it 16 inches off the car...
Ok, I want to build a rear wing for this car. Underbody and front end aero are also a must, but I'm starting with the rear. Now, this specific car will run both rallycross events and road courses, so it'll be an interesting challenge to put any effective aero modifications on it - especially as an amateur like myself. Rallycross is low speed, has lots of sideways cornering (yaw), and road courses are the opposite. An extremely aggressive airfoil might perform great for low speed rallycross, but incur separation, heavy drag penalties, and become less efficient at high speed. By contrast, a more conservative profile (and placement on the car) would sacrifice low speed downforce for better flow at 100mph. More than likely, the cost effective solution (since I can't afford two airfoils) will be a conservative shape that performs well up to say 125mph, with adjustable angle of attack for track types. It's the boring and responsible solution but I'm not giving up there. I'd like to have two sets of end plates - one intended for heavy yaw conditions and lateral stability (rallycross) and one for high speed efficiency (road course). That's the idea anyway. I'll be sure to post pictures of what comes!